The Importance of Plastic Injection Molds in Modern Manufacturing
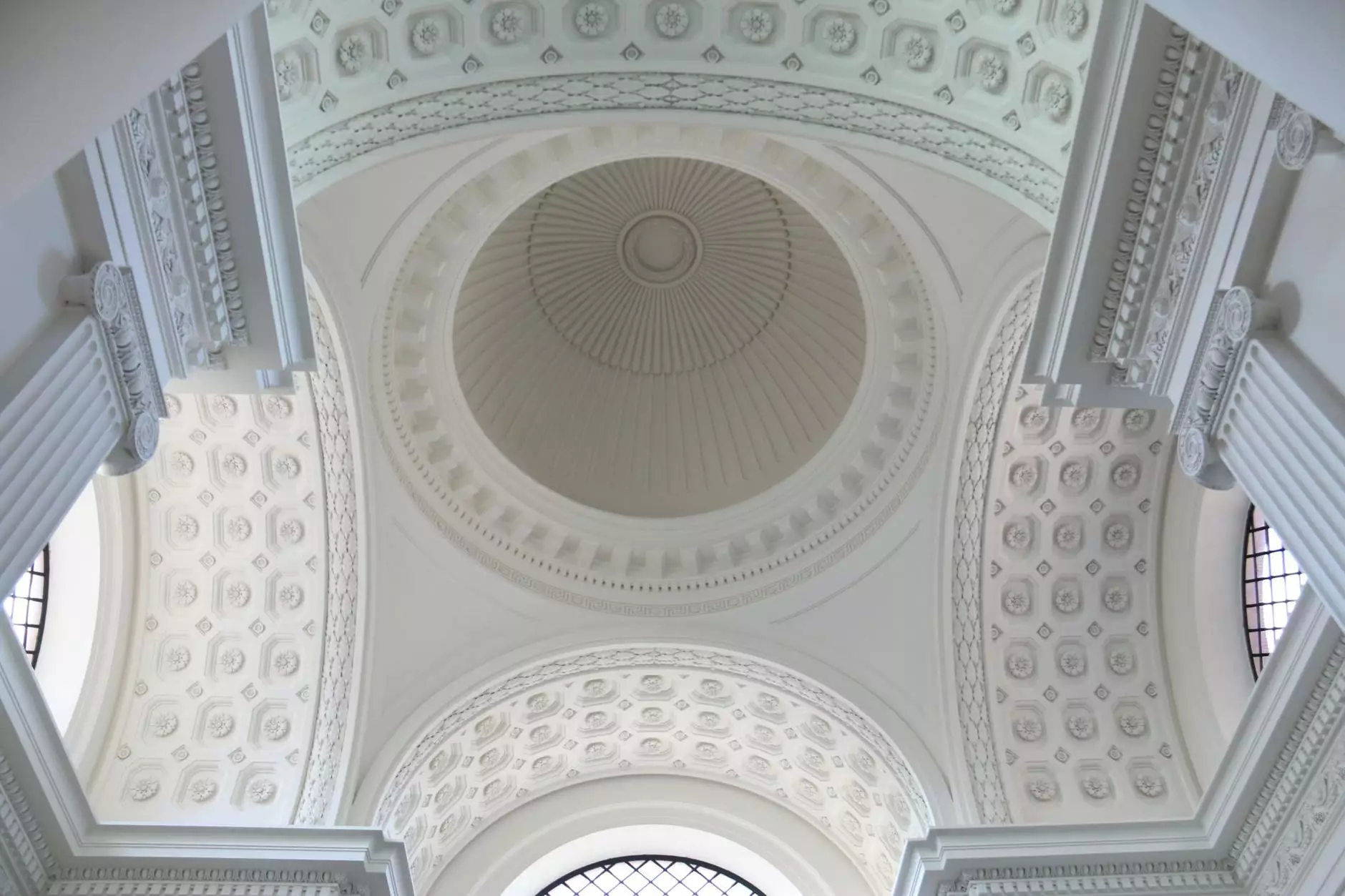
In today's rapidly evolving industrial landscape, the role of plastic injection molds cannot be overstated. They are fundamental in the production process of a vast array of plastic products that we encounter in our everyday lives. From automotive components to consumer electronics, plastic injection molds serve as the backbone of modern manufacturing techniques.
Understanding Plastic Injection Molding
Plastic injection molding is a manufacturing process for producing parts by injecting molten material into a mold. The process involves the use of a machine, which heats the plastic and then injects it into a mold cavity under pressure. Once cooled, the mold is opened, and the solidified part is ejected. This technique is lauded for its efficiency in mass production and its capability to produce complex shapes with high precision.
How Plastic Injection Molding Works
- Material Selection: Common materials include thermoplastics and thermosetting plastics.
- Mold Design: Designing a mold that accounts for part shape, size, and production volume.
- Injection Process: The plastic pellets are heated, melted, and injected into the mold.
- Cooling: Allowing the material to cool and solidify before the mold is opened.
- Ejection: The finished part is ejected from the mold and prepared for further processing or assembly.
The Benefits of Using Plastic Injection Molds
Investing in plastic injection molds offers a myriad of advantages that can significantly enhance a business's productivity and output quality. Here we’ll explore some of the key benefits:
1. High Efficiency and Production Speed
One of the standout features of plastic injection molds is their ability to produce a large number of parts in a relatively short time frame. The automated process allows for quick cycle times, meaning businesses can ramp up production and meet customer demands swiftly.
2. Design Flexibility
With modern CAD (Computer-Aided Design) technologies, manufacturers can design intricate mold geometries that enable the production of complex parts that would be impossible to create with other manufacturing processes. This design flexibility leads to innovative product development.
3. Cost-Effectiveness for Mass Production
Though the initial investment in plastic injection molds can be high, the cost per unit decreases significantly with mass production. This makes it an economical choice for companies looking to produce large volumes of the same component.
4. High Precision and Consistency
Injection molds provide exceptional tolerances and uniformity in finished products, which is vital for sectors like automotive and medical devices where precision is crucial. This consistency reduces the need for extensive quality control processes.
5. Reduced Waste
Compared to other forming processes, plastic injection molding generates minimal waste. Any excess material can often be reused, which is not only cost-effective but also environmentally friendly.
Applications of Plastic Injection Molds
The realms of application for plastic injection molds are vast and varied. Industries across the spectrum utilize this technology to manufacture their products:
- Automotive Industry: Production of dashboards, panels, and other components.
- Consumer Goods: Items such as toys, kitchen utensils, and packaging.
- Electronics: Enclosures for devices, connectors, and components.
- Medical Devices: Components for syringes, inhalers, and surgical instruments.
Choosing the Right Plastic Injection Mold Provider
Selecting a reputable supplier for plastic injection molds is critical to ensuring quality and reliability in your manufacturing process. Here are some essential considerations:
1. Experience in the Industry
Look for a manufacturer with a proven track record and substantial experience in injection molding. Experience often translates into better design, manufacturing practices, and problem-solving capabilities.
2. Quality Assurance Processes
Inquire about the company’s quality control measures. A reliable provider should adhere to industry standards and regularly conduct inspections to ensure that the molds meet specified tolerances.
3. Customization Capabilities
Your project may have unique requirements. A good provider will offer customization options to tailor molds specifically for your products, catering to your design specifications and production needs.
4. Technical Support and Services
Choose a partner who provides excellent customer support and services, including mold maintenance and troubleshooting, ensuring smooth operations throughout the lifecycle of the mold.
The Future of Plastic Injection Molding
The future of plastic injection molding looks bright, fueled by advancements in technology and material science. Innovations like 3D printing of molds, automation through robotic systems, and the use of sustainable materials are redefining the boundaries of what's possible in this manufacturing process.
The integration of Industry 4.0 with real-time data monitoring and analysis will further enhance efficiency, allowing for predictive maintenance and optimization of production schedules.
Conclusion
In conclusion, plastic injection molds stand at the forefront of modern manufacturing, enabling mass production with high efficiency, consistency, and precision. As businesses continue to evolve and adapt to new technologies, the importance of quality molds will only increase. Companies investing in reliable, innovative suppliers of plastic injection molds like deepmould.net will be well-positioned to thrive in the competitive landscape of the manufacturing industry.
By understanding the implications of this manufacturing method, businesses can leverage the advantages of plastic injection molds to streamline their operations, reduce costs, and deliver high-quality products that meet the demands of the market.