Understanding the Manifold Valve Function in Industrial Applications
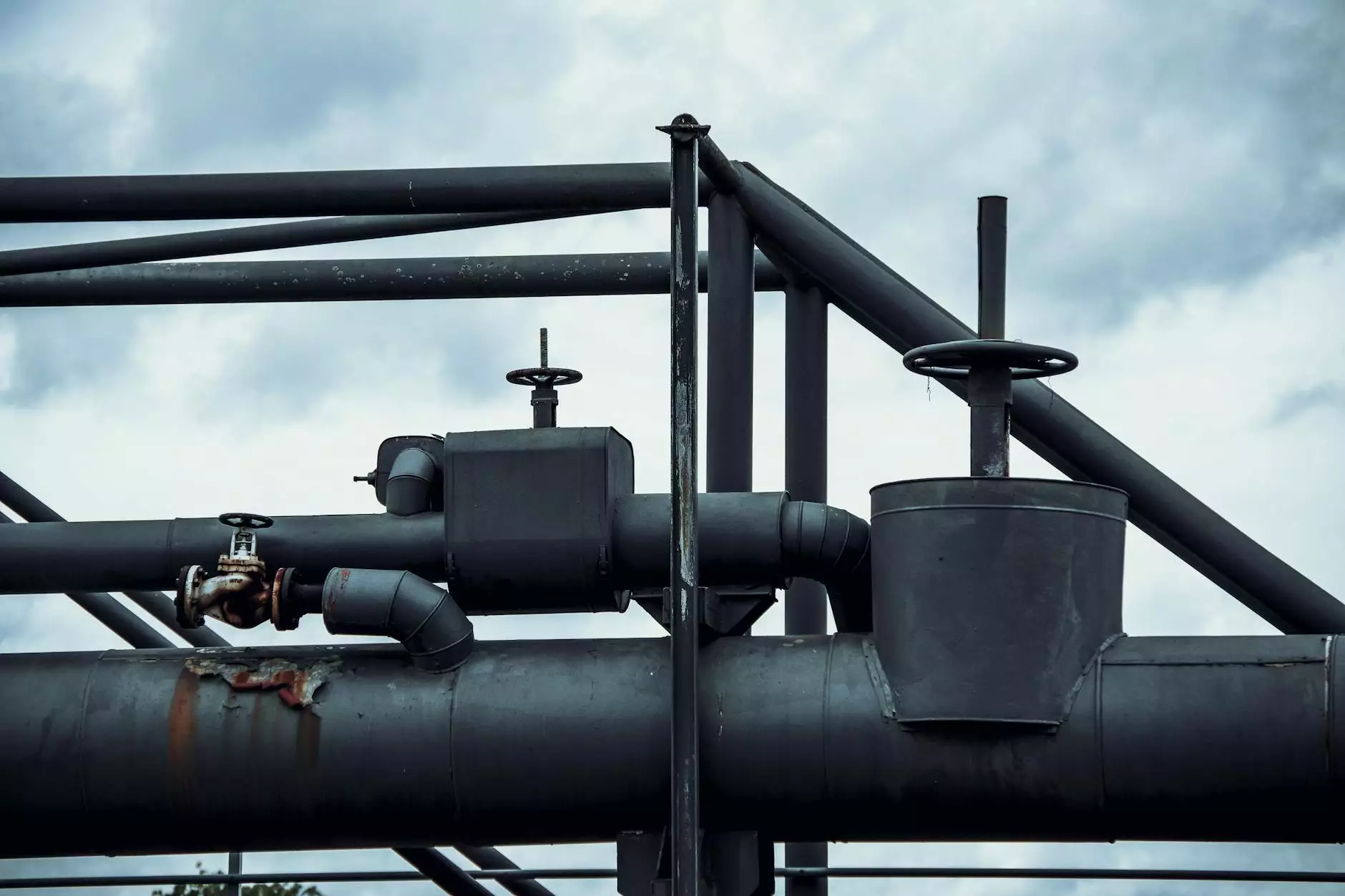
The importance of manifold valves in industrial settings cannot be overstated. These essential components play a significant role in controlling fluid and gas flow, ensuring safe and efficient operation of systems. In this article, we delve deep into the manifold valve function, its types, benefits, and various applications that highlight its critical contributions to industry.
What is a Manifold Valve?
A manifold valve is a type of valve that consolidates multiple pathways or connections into a single assembly. This design simplifies the flow of fluids or gases in complex plumbing or piping systems. By allowing for coordinated control, manifold valves streamline operations and enhance the efficiency of systems.
The Function of Manifold Valves
At the heart of the manifold valve function is its ability to manage the flow of different substances while providing safety and efficiency. The primary functions include:
- Flow Control: Manifold valves regulate the volume and pressure of fluids or gases within systems.
- Isolation: They provide the capability to isolate specific sections of piping without shutting down the entire system.
- Pressure Relief: Some manifold valves are equipped with pressure relief features to prevent system failure.
- Multi-Path Routing: Manifold valves facilitate the redirection of flow through multiple ports, providing versatility in operations.
Types of Manifold Valves
Manifold valves come in various types, each designed to fulfill specific functions in industrial applications. Below is a detailed description of different types of manifold valves commonly used:
1. Block and Bleed Valves
These valves allow for the complete isolation of a section of the system while providing a bleeding option to relieve pressure before maintenance. The block and bleed functionality is critical for safety during repairs.
2. Three-Valve Manifolds
A three-valve manifold consists of three valves that permit pressure measurement and system monitoring. It provides unparalleled accuracy in determining pressure levels in various processes.
3. Five-Valve Manifolds
These are more complex than their three-valve counterparts and are employed in advanced applications, allowing for exceptional control of flow and pressure measurements. The five-valve configuration enhances operational safety and efficiency.
4. Proportional Control Valves
Proportional control valves adjust flow based on the input signal, providing precise control over the system. These valves are essential for applications requiring fine-tuned adjustments to flow rates or pressure.
Benefits of Using Manifold Valves
The adoption of manifold valves in industrial applications offers numerous advantages:
- Simplification: Reduces the complexity of piping systems, allowing for more straightforward installation and maintenance.
- Efficiency: Facilitates easier adjustments and monitoring of flows, improving operational efficiency.
- Space-Saving: Consolidates components, saving valuable space in congested industrial environments.
- Safety: Incorporates safety features such as pressure release that enhance overall system safety.
- Cost-Effectiveness: Minimizes the number of individual fittings and valves needed, reducing material and installation costs.
Applications of Manifold Valves
Manifold valves are widely used across various sectors due to their versatility and efficiency. Here are some notable applications:
1. Oil and Gas Industry
In the oil and gas sector, manifold valves manage the flow of hydrocarbons through pipelines, ensuring safe and regulated operation while minimizing leak risks.
2. Aerospace
Aerospace applications require precision and reliability. Manifold valves are critical in controlling hydraulic systems that operate landing gear and flight control surfaces.
3. Chemical Processing
In chemical processing, manifold valves allow for the safe and efficient handling of corrosive substances, maintaining operational safety standards while enhancing process controls.
4. Water Treatment Facilities
Manifold valves are employed in water treatment plants to manage chemical dosing and flow rates, contributing to better water quality and treatment efficiency.
5. Pneumatic Systems
In pneumatic applications, manifold valves control the flow of air and other gases, optimizing performance in automation processes and machinery operations.
Choosing the Right Manifold Valve
When selecting a manifold valve, consider the following factors to ensure optimal performance:
- Material Compatibility: Choose materials that are suitable for the fluids or gases being handled.
- Pressure and Temperature Ratings: Ensure that the valve can withstand the conditions of your specific application.
- Flow Requirements: Analyze the flow and pressure requirements to select the appropriate valve type and size.
- Certification Standards: Check for necessary certifications, especially in industries such as pharmaceuticals and food processing.
- Ease of Maintenance: Consider valves that facilitate easy operation and maintenance for prolonged service life.
Conclusion
The manifold valve function is a pivotal element in modern industry, streamlining processes and enhancing safety standards across various applications. Understanding the types, benefits, and appropriate usage of manifold valves is essential for optimizing performance and reliability.
At techtubes.in, we offer a comprehensive range of valves, including check valves, ball valves, forged pipe fittings, and a variety of fittings tailored to meet your specific needs. With our commitment to quality and service, we ensure you have the right solutions for your operational challenges. Elevate your business operations today with our state-of-the-art manifold valves and other high-quality products!